OSHA high visibility requirements explained
Within the Occupational Safety and Health Administration (OSHA), the term "high visibility" refers to protective gear – commonly vests, pants, or jackets – that utilize fluorescent or retro-reflective colors to make workers more visible in hazardous work environments. OSHA high visibility requirements are a subset of the broad category of "personal protective equipment" (PPE). PPE is the last line of defense in a hierarchy of workplace safety measures; rather than seeking to directly address environmental or equipment-related risks, PPE protects the individual worker.
OSHA has not issued a uniform standard outlining the agency’s requirements for high visibility wear, although a variety of regulations address the issue across various industries. For example , OSHA’s Road Construction Temporary Traffic Control regulation requires workers in the "attenuation vehicle" leading a moving operation to wear "both fluorescent orange or lime yellow-green apparel and retro-reflective apparel." Other regulations, like its Steel Erection regulations or Electrical protective equipment regulations, touch on the need for high visibility apparel while discussing PPE more broadly.
OSHA has found that high visibility wear is a necessary component of an effective approach to managing risks. The agency has identified more than 100 worker fatalities in the road construction industry between 2003 and 2005, and experts believe greater adoption of high visibility wear would prevent the deaths of more than 50 U.S. highway construction workers annually. Similar benefits are associated with enhancing the use of high visibility garments in other workplaces.
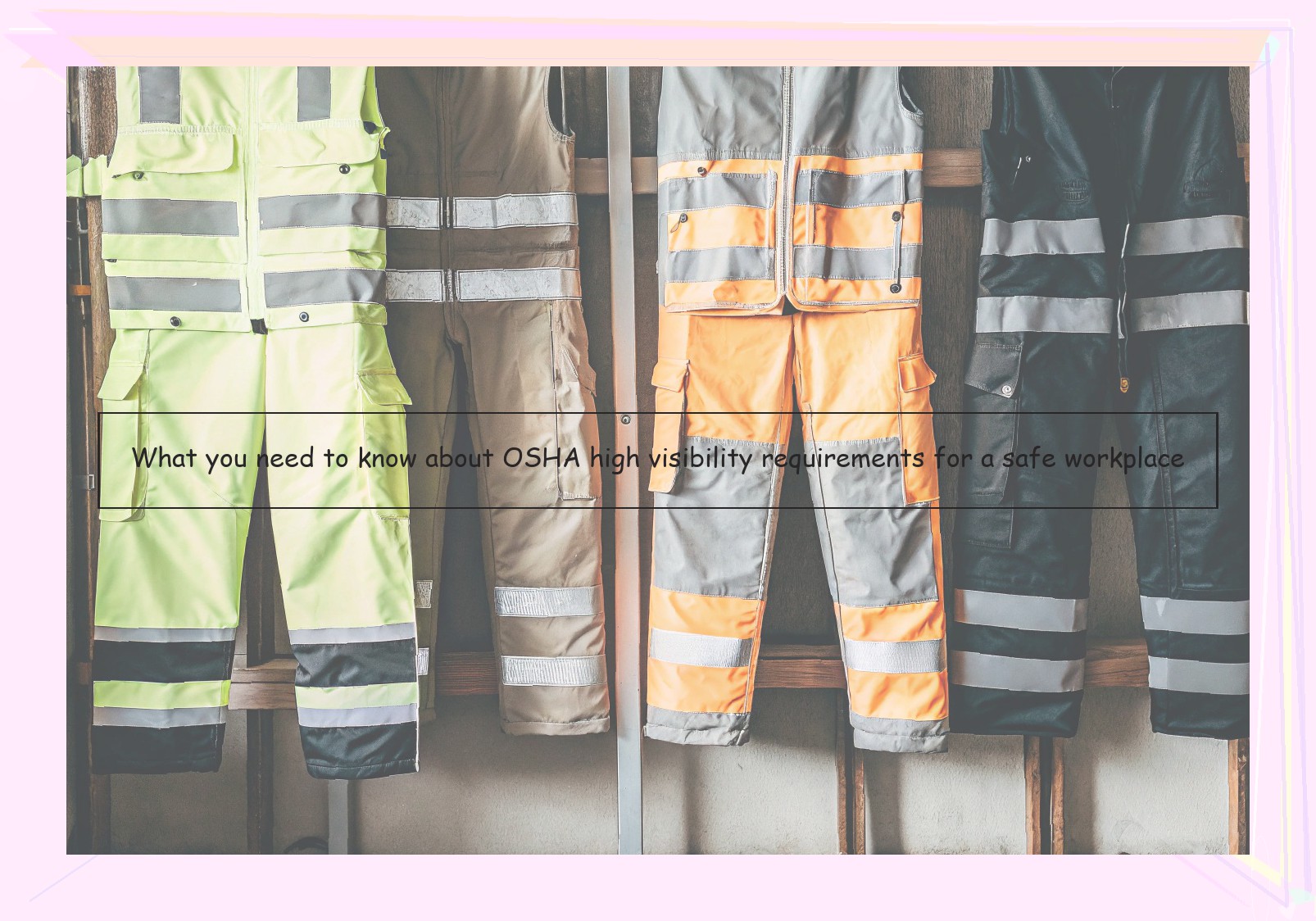
Who needs to meet high visibility standards
When it comes to high visibility standards, a large number of employees will be required by the Occupational Safety and Health Administration to comply. Although the requirements were imposed primarily to protect construction workers, they can be applied to people who do a number of different jobs. This will include those who move equipment for construction sites and workers who use grading equipment, power excavators, bulldozers, and tunneling equipment.
Along with this will be those who work along roadways or railway lines. Examples of these would be utility workers, survey crews, flaggers, emergency responders, and more. Any other workers who need to be visible in their line of work will also be required to follow the high visibility standard. This can include anyone who uses common tools and equipment associated with truck motor vehicles, such as dump trucks, payloaders, and loader backhoes.
Components of the standards for high visibility
For any worker operating in situations where there are moving vehicles or equipment, such as road construction or highway maintenance sites, the U.S. Occupational Safety and Health Administration (OSHA) requires wearing adequate high visibility clothing, including safety vests, jackets, outerwear, and pants.
When defining quality, OSHA frequently refers to the American National Standards Institute (ANSI) to ensure the right level of brightness, color, and retro-reflective material are used cross-industries for workers that "need to be conspicuous to be seen". These materials and colors let motorists know pedestrian workers are present, hopefully alerting them to slow down and avoid a collision.
The requirements may also differ from night to day. For example, some definitions for vests require a reflective vest during the day and possibly reflective outerwear at night to ensure workers are visible. Vests, jackets, and pants may need to be ANSI 107 Class 2 sections for highway work, while only ANSI 107 Class 1 is required for driveway work. For off highway operations, wearing a Class 2 vest may be required, and the garment may need to pass an ANSI test for "retroreflectivity" to ensure the brightness and color are vivid enough to be located at night.
OSHA also requires workers to wear additional ANSI Class 3 materials where the threat for hazardous situations is especially high. This includes work on roadways with traffic 50 miles per hour or more with no barrier, or on roadways where traffic is 50 miles per hour or less with a barrier.
The ANSI standards (844) used for classifying such clothes, reference garments with trim colors, which act as a barrier in conjunction with the primary reflective clothing material. For example, ANSI 107 Class 2 garments must be lime-yellow and red as well as black or blue. ANSI 107 Class 3 requires fluorescent orange-red, lime-green, and silver, where ANSI 207 vests must be fluorescent lime yellow or orange red.
A good rule of thumb is: The more roadway, traffic, and reflectivity hazards, the more visibility required.
How high visibility equipment boosts safety
High visibility gear is not just a requirement for many work sites, it is a requirement for safety. Research shows that the use of high visibility materials significantly reduces overall individual injuries. It makes sense if you think about it: when someone is more visible, they are easier to avoid and less likely to be injured.
In the United States, Department of Transportation funding has been reserved for evaluating high visibility vests and uniforms, specifically how they affect an area and whether they have increased visibility for the workers wearing them. They found that larger garments, materials and markings were highly visible to drivers, and that daytime and nighttime visibility of these uniforms and vests were reduced significantly when they were not highly visible.
In another government report, they found that "wearing high visibility clothing is widely considered to provide superior detection of workers by motorists in work zones." High visibility gear creates "a contrast against a particular visual environment" and "like workers in other settings, those in the construction industry benefit when a sufficient contrast is created between workers and their environment."
The same study looked at the effects of colors on those wearing them and those spotting them. They showed that "although workers with orange garments were technically at a higher risk when compared to those with fluorescent yellow garments the differences were modest and the effect statistically negligible."
Of all the colors tested, "yellow green was consistently recognized most rapidly. The color also resulted in fewer misses. In no condition did the yellow green result in a higher rate of false positives." Overall, "participants tended to respond more quickly in general to yellow green."
Yellow green is the second most popular color compromised of high visibility clothing after orange, but is one of the better ones for increasing safety.
Standards for compliance with OSHA regulations
For the purposes of compliance with the Occupational Safety and Health Administration (OSHA) regulations, the American National Standards Institute (ANSI) classifications for high visibility apparel are divided into 3 classes as follows: Class 2 – can be identified as an intermediate level of protection (typically requiring full or substantial compliance) for workers between the hazard and public area (i.e. work zone), performing tasks near traffic, or surveying on roadways. Class 3 – can be identified as an advanced level of protection (typically requiring full or substantial compliance) for workers between the hazard and public area (i.e. work zone), working with traffic, close to public access , and performing tasks that distract from the view of approaching traffic on a roadway. In general, there are three ways in which companies and employees can ensure compliance with OSHA regulations: To ensure compliance with ANSI, high visibility apparel must be labeled as either an ANSI 107-2010 "Type R (Roadway) or Type P (Public Safety)", or ANSI/ISEA 107-2004 "Class 2 or Class 3" garment. For ANSI/ISEA 107 garments that do not include ANSI labels, the compliance standard must also be indicated on the manufacturer’s label. In general, high visibility work apparel needs to be ANSI class 2 or 3 levels of protection and includes safety vests, jackets, and/or rain gear used by employees.
Challenges and solutions for implementing the standards for high visibility
Safety managers confront a wide variety of issues when it comes to the implementation of OSHA high visibility requirements within their workplace. The most common challenge is some variant of "but our employees don’t want to wear that hellish lime-green vest!" Even industries that have voluntary vests soon find that once the thought of a new color (especially one so eye-popping) is raised, that objection surfaces.
First, there is no such thing as a "hellish lime-green vest;" there are vests in thousands of colors, including black and gray, and even some in red, yellow, and blue. Second, needing your employees to be seen (and therefore provided with gear that permits the same) is not, in fact, an unreasonable request. Third, employers don’t have to mandate it. If employees can be persuaded to wear safety gear voluntarily, the employer need only provide it and ensure that the selected item(s) meet ANSI specifications.
The second most common issue is that of cost. Some managers struggle with how to measure the business imperative below the level of "that’s nice" in a risk assessment. Others anticipate an extraordinary financial hit (for example, the very real cost of replacement of gear lost or damaged). Since the ANSI/SEA 107-2015 revisions, the ANSI requirements for hats/caps have been loosened, which could possibly save money, but other required elements cannot be eliminated. Still other employers submit unfounded requests for prototypes or for help bringing materials in compliance with ANSI specifications. The most important note here is that without employer buy-in and the support of the safety manager and HR, implementation is never going to (and doesn’t need to) be perfect from Day 1.
But it can be good enough: prepare those cost analyses, ask how much equipment needs to be procured, and survey employees about their perceptions of safety issues relating to the identified hazards. Once the appropriate gear has been identified (again based on ANSI specifications), determine what the actual cost will be to the company, and graph that against the anticipated price of an injury claim.
Finally, be certain to build in the fact that these are minimum standards – there is nothing preventing employers from providing gear that exceeds ANSI specifications. The most effective way to convince recalcitrant workers to wear high visibility gear that they don’t want to wear is to give them something that is more comfortable. For example, ANSI/ISEA specifications provide for garments with 3M 8712 tape as providing 10 percent more conspicuity than 3M 8710 tape; therefore, a cost/benefit analysis of the increased price of 8712 tape may well convince employers to move from the standard to the premium.
Trends driving future standards for high visibility
Emerging technologies in workplace safety gear, such as the development of intelligent materials and the integration of technology into safety gear, will continue to impact high visibility requirements. High tech fabrics, for instance, may include photoluminescent dye that reacts with ultraviolet light at dusk or dawn to increase visibility. Other smart materials can change color with temperature, making them visible during temperature differentials. The incorporation of GPS into vests for employees working in remote areas may help improve situational awareness and reduce accidents when employees are out of line of sight. Yet another trend could be a shift toward reflective material that lights up when exposed to ambient light or certain colors of light. Every year it seems like designers and researchers come up with new ideas that could increase visibility, both effectively and fashionably.
Beyond textiles , there is promise in the use of augmented reality to meet high visibility requirements. Augmented reality systems are designed to superimpose images over the user’s real-world view so users can view themselves, their gear or surroundings with a level of interaction and detail unavailable from the naked eye. Application of augmented reality to safety gear might include heads-up displays for construction workers that show relevant data in the worker’s field of view (similar to Google Glass), or construction vehicles that project navigational instructions directly onto the ground.
Continued advancement in this area is not hard to imagine as more companies explore new ways of incorporating augmented reality technology in their gear. If such technologies are proven to be more effective, it would not be surprising if OSHA begins to mandate their use where appropriate.